Tragic death sparks safety review
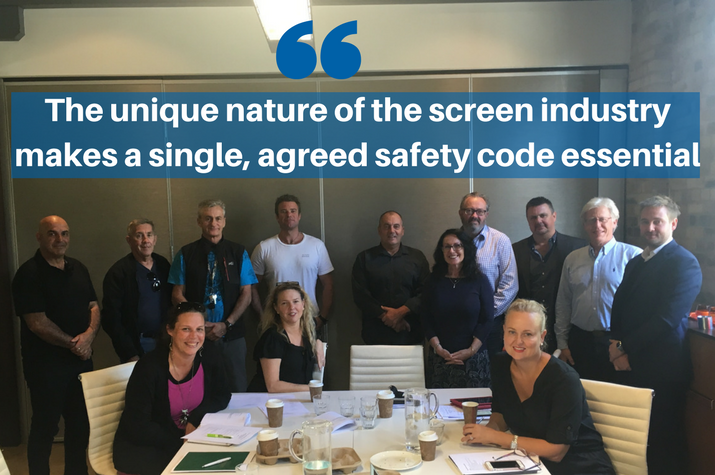
The first meeting of the Safety Review in Brisbane in May
The death of stunt performer Johann ‘Yogi’ Ofner brought the industry together to commence a review of safety in the screen industry.
On January 23, Johann ‘Yogi’ Ofner suffered a fatal injury while filming a scene involving a firearm on the set of a music video in Brisbane. Ofner was, by all accounts, a talented performer, with a promising career ahead of him. He was also a beloved son, partner and father to six-year-old daughter, Kyarna Le Lani Ofner.
The tragic incident is still under investigation by Queensland Workplace Health and Safety but what we do know is that it gave the screen industry a serious wake-up call.
“On January 23, something happened in our industry that can’t be ignored. We lost one of our own,” says Michelle Rae, director of MEAA Queensland and the MEAA National Stunt Committee. “That made the industry stand up and say, We need to have guidelines that are reflective of the changes in the Workplace Health and Safety Act, and also within the industry.”
In the wake of Ofner’s death, representatives from every state screen agency, MEAA, Screen Producers Australia and industry professionals formed a Safety Review and met to begin the lengthy and complex process of overhauling the current safety guidelines.
“Back in 1983, the industry came together and said we need to have some guidelines as to how to act safely because we’re a little bit different to most industries – we actually try to make the unbelievable believable,” says Rae.
In 2004, the industry met to update those guidelines but was unable to reach consensus, which means the formal guidelines in place are more than three decades old. “Unfortunately, after all the work and energy that was put into updating the guidelines, we have a draft but nothing that was formally agreed upon,” Rae says. “That’s got to change because, as you can imagine, in 1983 we didn’t have all of the technology that we do now.”
Rae attended the first meeting of the Safety Review in Brisbane in May. She says it was constructive and there was strong support for developing a single, comprehensive manual which is easy to understand and applies to all screen productions. “Our industry includes a huge range of working environments, specialist skills and demands. The potential for workers to be put in dangerous situations is high. There are also less-obvious hazards that can have just as much impact, like physical and psychological stress, fatigue and bullying. We need an industry safety code that we can use to keep everyone safe and healthy.”
Following the meeting, performers, producers and crew were given the opportunity to provide detailed feedback on every section of the new Safety Code – from action vehicles, animals and armoury to special effects, stunts and shooting.
Safety supervisor Joe Pampanella has been heavily involved in the review process. “It’s human nature to take action the minute there’s a disaster,” he says. “And it’s not only in this industry. It happens in manufacturing, it happens on building sites.”
Pampanella began his career as a stunt performer in the 1980s. In the 1990s he studied Occupational Health and Safety at TAFE and returned to the film and TV industry in 1999 as a safety supervisor. He has been working steadily in the field ever since.
“I don’t think people don’t take safety seriously,” he says. “It is a big monster to control but, in my experience, employers and employees don’t purposely do things to injure people or be unsafe. Often it’s the pressures of the job – to get something done quickly, to get it done cheaply, or just to get it done for the sake of the production. Ultimately, this is an industry where you’re only as good as your last performance.”
The role of the safety supervisor is essential in such an environment, says Pampanella. “For example, if I’m behind the camera as a grip or as an electrics and the director says to me, ‘I need to put a light on that roof’, my job is to get that done. But, in my effort to get the job done, and because it’s such a quick environment, I may not have time to stop and do a proper risk assessment. What safety supervisors do is hover around and go, Okay, they’re going up on the roof – how are they going to get there? What are the risks involved? How are we going to manage these risks safely but still get the job done?”
Pampanella believes there needs to be a systematic approach to performing hazardous actions on set. “The people who put together the ’83 document were very astute and had a lot of foresight, because it is actually a really good document for its time. The unfortunate thing is it hasn’t been upgraded to meet the OH&S standards of today.”
The unique nature of the screen industry makes a single, agreed safety code essential, he says. “The industry is a whole bunch of little businesses. One grip company is totally separate from another grip company and they do things differently. This new safety code is about getting a whole lot of people to say, We will all use this as our guide, as our minimum standard. For example, when they work at heights, they’re all going to do the same risk assessments. When they’re using plant and equipment, they’re going to use the same process as required in the safety code.”
While the code is largely aimed at heads of departments, Pampanella says it’s vital for performers and crew to be familiar with it, as well, before they go on set. “Individual employees have a responsibility for their own safety and for the safety of those around them. It would really be handy to look through the code in the particular area that you’re going to be working in. And, probably more importantly, it will show you that you have the power and the right to go, Well, hang on, I’m not happy about this. Can you explain to me how this is going to be done safely? If you’re familiar with the code, you’re in a much better position to ask questions and be sure you’re happy with what you’re doing.”
A large volume of feedback came through online consultation and member meetings in the middle of the year. The Safety Review working group has been examining the feedback in detail and will discuss progress before the end of the year, with work to be completed on a unified industry code in 2018.
This article was originally published in the Spring 2017 issue of The Equity Magazine.